Lean Six Sigma Black Belt Course Overview
- Mastery of advanced Lean Six Sigma tools and methodologies
- Proficiency in statistical analysis for data-driven decision-making
- Ability to lead cross-functional teams and manage complex projects
- Skills to mentor and coach Green and Yellow Belts in process improvement initiatives
Prerequisites of the Lean Six Sigma Black Belt Course
- Have completed and passed the Lean Six Sigma Yellow Belt Course
- Have completed and passed the Lean Six Sigma Green Belt Course
- Have basic knowledge of Lean Six Sigma
Who should attend this Lean Six Sigma Black Belt Course?
- Senior Managers
- Project Managers
- Quality Directors
- Consultants
- Continuous Improvement Managers
- Quality Assurance Managers
Course Structure
- In the first 3 days, we will cover the essential materials needed to understand Lean Six Sigma Black Belt
- The remaining 2 days will cover the essential materials needed to take the Lean Six Sigma Black Belt exam
Lean Six Sigma Black Belt Course Outline
- What is Lean 6 Sigma?
- Lean 6 Sigma Belts
- Processes
- Customers, Value, and Waste
- Key Metrics
- What is DMAIC?
- Define
- Measure
- Analyse
- Improve
- Control
- Lean Triad
- Voice of the Customer (and CTQ’s)
- SIPOC
- Value Stream Analysis
- Heijunka
- Variation and SPC
- Defects and Process Capability
- Identifying the Root Cause(s)
- Solving Problems
- Introduction to Kaizen
- Lean Teams
- DMAIC
- 3Cs
- 8Ds
- Plan Do Check Act
- Kaizen
- Design for Six Sigma (DFSS)
- Terminology
- Data Types
- Normal Distribution and Standard Deviation
- Process Capability
- Role of the Lean Manager
- Work Cells
- High Performing Teams (HPTs)
- Rapid Action Teams (RATs)
- Visual Management
- Bruce Tuckman’s Group Development Model
- Emotional Cycle of Change (ECOC)
- Personality Styles
- Dealing with Resistance
- Green Belt Risk Management
- FMEA: Failure Mode and Effects Analysis
- Define Phase
- Measure Phase
- Frequency Distribution Tables
- Bar Charts and Histograms
- Pareto Charts
- Box and Whisker Plots
- Normal Distribution and Control Charts
- Calculating Process Efficiency
- Scatter Diagrams and Regression
- Analyse
- Process Maps
- Process Map Levels
- On the Ground Instructions (OTGIs)
- Value Stream Maps
- What is a Value Stream?
- Creating the “As Is” VSM
- Investigating and Understanding the Process
- Headache Tablets: Value Stream Mapping
- Creating a VSM: Process Borders Definition
- Using Swim Lane Diagrams to Identify Logical Process Blocks
- Process Boxes
- VSM Metrics
- Square Wave
- Kaizen Burst
- Creating an Improved Process
- Layout Diagrams and Headache Tablets
- Heijunka
- Solutions Identified, Selected, Planned, and Implemented
- Standardisation and Documentation
- Communications and Training
- Embed the change
- Measure the gain
- Close the project
- Black Belts’ Place in the Business
- Black Belt Skill Set
- Green Belts’ View of the World
- Black Belts’ View of the World
- How does the Industry Identify Black Belts?
- Who does the Black Belt Work with?
- Case Study
- How the Black Belt helps the Green Belt During DMAIC?
- Measure Phase
- DMAIC Programmes
- Governance
- Risks Lie in Two Areas
- Who Should Handle Risk?
- DMAIC Risk
- A view of Business Risk Management
- Basic Risk Management Procedure
- Business Risk Management in a Nutshell
- In a Nutshell
- Task & Work Cells
- Flow Improvement Objectives
- Practical Layout Design
- Characteristics of Adult Learners
- Three Common Learning Styles
- Preparing the Training
- Top Tips
- Case Study
- Introduction and SPC Refresh
- Common Terminology
- Flow Improvement Objectives
- Measuring Uncertainty
- Minitab Run-through
- Process Capability: Review from Green Belt
- Introduction to Hypotheses Testing
- Working with Hypotheses Tests
- Hypothesis Test Roadmap
- Anderson Darling Normality Test
- To Open the Worksheet
- The Results
- Testing for Means
- t-tests Consider More than Just the Means…
- t-test Exercise
- Z test
- Testing for Medians
- Where Could I Use Median Tests?
- Median Hypothesis Tests
- Testing for Standard Deviation (Variance)
- Equal Variance Hypothesis Tests
- Exercise: Test for Equal Variance
- Interpreting the Results
- Using Bartlett’s Method
- Testing for Proportions and Percentages
- Proportions and Percentages Hypothesis Tests
- Scenario
- Abbreviated Instructions
- Reviewing the Results
- Scenario
- Abbreviated Instructions
- Interpreting the Results
- Required conditions for ANOVA
- The ANOVA “family”
- ANOVA Terminology
- Hypotheses Tests and One-way ANOVAs
- Exercise - One-way ANOVA
- Exercise - Multi-way ANOVAs
- General Points
- Sample Size
- How a Greater Sample Size Reduces Uncertainty?
- Case Study
- Overview of DOE
- Where to Use Design of Experiments?
- DOE Terminology (1)
- Design of Experiments Flow Diagram
- Walkthrough: SB Glass Co
- Step 1: Investigate the Process
- Step 2: Gather Data
- Recording the Data: Building the Worksheet
- Minitab Creates an Initial DOE Worksheet
- Team Completes the Worksheet
- Teams’ First Analysis of the Data
- Minitab does its Stuff
- Overview
- Normal Distribution
- Binomial Distribution
- Poisson
- Exponential
- Weibull
- Introduction and Refresher
- Key Control Charts
- Data Collection Planning for Control Charts
- General overview
- Key Metrics
- Using Lean Metrics
- Overview
- Understanding Gauge R&R
- Minitab Walkthrough
- Modelling Queues
- Psychology of Queuing
What ‘s Included
Lean Six Sigma Yellow Belt Examination
Lean Six Sigma Green Belt Examination
Lean Six Sigma Black Belt Examination
World-Class Training Sessions From Experienced Instructors
Lean Six Sigma Black Belt Certificate
Exam
Lean Six Sigma Black Belt Exam
Ways to take this course
Classroom Training
Face-to-face sessions led by expert instructors, fostering interactive learning experiences and collaboration among delegates.
Online Instructor-Led Training
Live virtual classes led by experienced trainers, offering real-time interaction and guidance for optimal learning outcomes.
Online Self-Paced Training
Flexible learning at your own pace, with access to comprehensive course materials and resources available anytime, anywhere.
On-Site Training
Customised courses delivered at your location, tailored to your specific needs and scheduling preferences.
Lean Six Sigma Black Belt Calender
Lean Six Sigma Black Belt
£4595
1st July 2024
10th July 2024
(10 days)Virtual
Lean Six Sigma Black Belt
£4595
8th July 2024
17th July 2024
(10 days)Virtual
Lean Six Sigma Black Belt
£4595
15th July 2024
24th July 2024
(10 days)Virtual
Lean Six Sigma Black Belt
£4595
22nd July 2024
31st July 2024
(10 days)Virtual
Lean Six Sigma Black Belt
£8995
29th July 2024
7th August 2024
(10 days)Maidstone
Lean Six Sigma Black Belt
£8995
8th April 2024
17th April 2024
(10 days)Southampton
Lean Six Sigma Black Belt
£8995
23rd September 2024
2nd October 2024
(10 days)Southampton
Lean Six Sigma Black Belt
£8495
8th January 2024
17th January 2024
(10 days)London
Worldwide Learning Experience
These courses cater to learners worldwide, offering flexible options to fit your schedule and location.
Learning Path Towards Success
Explore
Dive into our comprehensive courses to find the best fit for your career goals.
Study
Avail our high-quality learning resources to scale up your career.
Practice
Gain hands-on experience through practical exercises, assignments and case studies.
Succeed
Achieve the skill set to attain a competitive edge in the job market.
Frequently Asked Questions
What is the difference between Black Belt and Green Belt Certification?
Black Belts are equipped to lead larger, more complex improvement projects and mentor Green Belts.
Is prior Lean Six Sigma experience required to attend the Black Belt Course?
Yes, delegates are required to have completed the Green Belt Certification or demonstrate equivalent experience.
How long does it take to complete the Lean Six Sigma Black Belt Course?
The Lean Six Sigma Black Belt Training is a 10-day course.
Can the Lean Six Sigma Black Belt Course be customised for specific industries?
Yes, the training can be altered to fit your organisation’s requirements.
Are there any prerequisites for taking the Black Belt exam?
Delegates must have passed the Lean Six Sigma Yellow Belt and Green Belt exams, in order to take the Lean Six Sigma Black Belt Course.
How can the Black Belt Certification benefit my career?
The Black Belt Certification demonstrates advanced expertise in process improvement, leadership, and project management, enhancing career prospects and earning potential.
What topics are covered in the Black Belt Course?
Topics include advanced statistical analysis, DMAIC methodology, project management, change management, and leadership skills.
Is the Black Belt Certification internationally recognised?
Yes, the Black Belt certificate is recognised worldwide as a mark of excellence in process improvement and quality management.
Can the Lean Six Sigma Black Belt Certification lead to job opportunities in senior management roles?
Yes, Black Belt Certification can qualify professionals for leadership positions in process improvement, quality management, and organisational development.
How can I prepare for the Black Belt exam?
Reviewing course materials, practicing advanced problem-solving techniques, and completing mock exams can help you prepare effectively for the Black Belt exam.
Find Your Best Course With Us
Discover the best courses tailored to your career goals. Get in touch with our support team for expert guidance.
Explore Our Client Saying
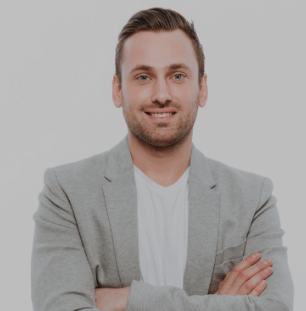
PRINCE2 Training has been an invaluable investment for us. The course was engaging, the material was excellent, and the instructors truly knew their stuff. It's not just about getting certified; it's about gaining skills that move our projects and our people forward.
Michael Carter
Project Director
The depth and clarity of the PRINCE2 Training have surpassed all our expectations. Our team now approaches projects with greater confidence and a solid framework, leading to more predictable and successful results. We're truly grateful for the transformation.
Samantha Wong
Project Lead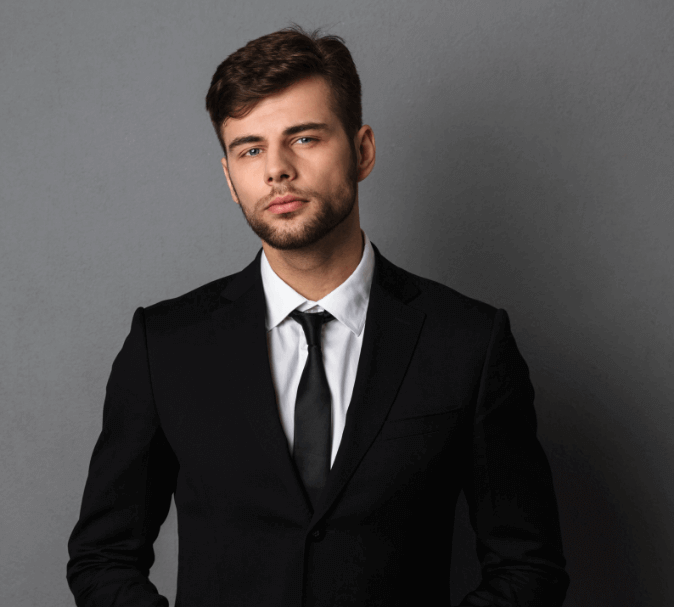
Choosing PRINCE2 Training was a pivotal decision for our team. The structured approach and practical insights have significantly improved our project delivery times and outcomes. It's clear why PRINCE2 is a leader in Project Management training!
David Patel
Senior Project Coordinator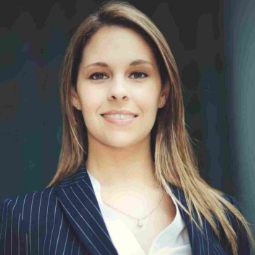
As a Project Manager, I can confidently say that registering for PRINCE2 Training was a game-changer for me. The comprehensive curriculum and practical approach gave me the tools and strategies I needed to excel in my role.
Emily Johnson
Project Manager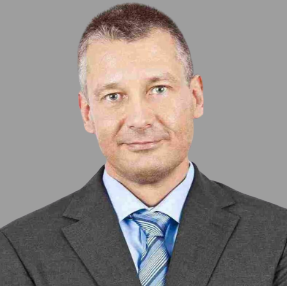
PRINCE2 Training was a game-changer for our team. The standardised approach to project management not only improved our efficiency but also enhanced collaboration and communication among team members. We're already seeing the positive impact of implementing PRINCE2 methodologies in our projects. Thank you for such a valuable learning experience!
Ada Richman
Project Governance Director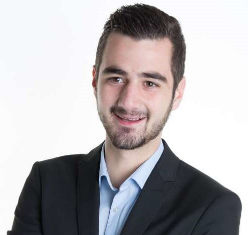
I can't say enough good things about PRINCE2 Training! The instructors were passionate about the subject matter and went above and beyond to ensure that all participants understood the material. Whether you're new to project management or looking to enhance your skills, I highly recommend investing in PRINCE2 Training.
Rod Stewart
IT Project Manager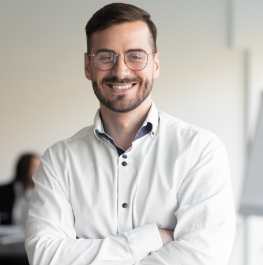
As someone with limited experience in project management, I found PRINCE2 Training to be incredibly valuable. The course content was well-structured and easy to follow, even for beginners like me. I appreciated the emphasis on practical application, which allowed me to immediately implement what I learned in my workplace.
Luca Bianchi
Program Director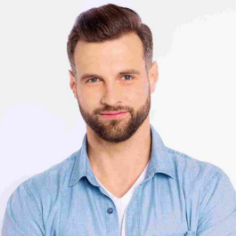
PRINCE2 Training provided me with the tools and techniques I needed to excel in my project management career. The practical exercises and real-world examples helped me apply the concepts to my job immediately. I'm grateful for the valuable skills I gained through this training program.
Henri Mitchell
Business Transformation Manager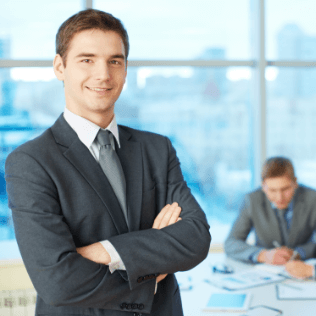
I had been looking for a comprehensive project management course, and PRINCE2 Training exceeded my expectations. The material was thorough, the instructors were engaging, and the support staff were always available to answer my questions. Thanks to PRINCE2, I feel confident tackling any project that comes my way.
Loren Crookes
Risk Management Specialist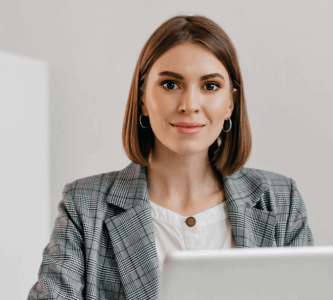
Registering for the PRINCE2 Training Was a Game-changer For Me! The Course Structure Was Well-organised, The Instructors were knowledgeable, and the hands-on approach really helped solidify my understanding of project management principles. Highly recommended!